控制系统是任何工业运营的中枢神经系统,管理温度调节到复杂机械运动的一切。多年来,这些系统已从基本的手动面板演变为与物联网(IoT)和自动化等先进技术无缝集成的复杂数字化解决方案。
在本文中,我们将探讨控制系统的演变历程、数字化集成如何改变规则,以及工业控制系统的未来发展方向。
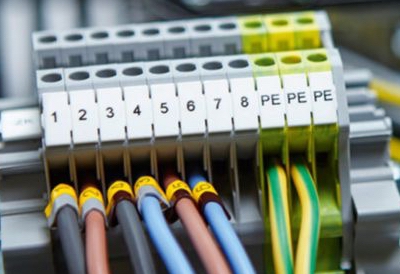
从基础面板到先进系统
历史上,控制系统由带有物理开关和旋钮的手动面板组成,操作员需要手动进行调整。虽然这些系统在当时是有效的,但它们通常属于劳动密集型,容易出现人为错误,并且缺乏有效管理现代工业流程所需的灵活性。
1.早期控制系统:
在20世纪中叶,工业控制通常使用基于继电器的逻辑和基本配电板实现。这些系统虽然可靠,但在处理复杂流程或适应实时变化方面的能力有限。
2.PLC的引入:
20世纪60年代,可编程逻辑控制器(PLC)的引入彻底改变了控制系统。PLC实现了许多以前手动处理任务的自动化,提高了效率,减少了人为错误,并增强了工业环境中的精确性。
3.SCADA的兴起:
20世纪70年代,监控与数据采集(SCADA)系统出现,实现了对流程的远程控制和监控。SCADA系统使操作员能够了解工厂运营情况,快速发现并解决问题。
现代控制系统:不仅仅是自动化
如今,控制系统已经远远超越了基础自动化。它们现在集成了数字技术,提供增强的控制、监控和数据分析功能。以下是现代系统如何重塑工业运营的方式:
1.物联网与实时监控:
物联网(IoT)为控制系统开辟了新的可能性,使其能够从各种设备、传感器和机器中实时收集数据。这种连接性允许基于实时数据进行持续监控和即时调整,从而提高效率和安全性。
2.与工业网络的集成:
现代控制系统设计为与其他工业网络无缝通信,包括制造执行系统(MES)、企业资源规划(ERP)软件,甚至先进的数据分析平台。这种集成使决策更智能,运营更同步。
3.远程访问与控制:
随着云计算和远程访问技术的进步,控制系统现在可以在世界任何地方进行管理。这对于拥有多个地点的行业或需要在非工作时间监控的系统尤其有益。
向数字化集成的转变
从手动面板到数字化集成的转变,在几个关键领域显著改善了工业控制系统:
1.增强的用户界面:
现代控制系统配备了直观的图形用户界面(GUI),以比传统系统更友好的方式为操作员提供实时数据和控制功能。这些界面支持触摸屏、视觉警报和自定义仪表板,提高了可访问性和易用性。
2.预测性维护与人工智能:
人工智能(AI)和机器学习现在被纳入控制系统,实现了预测性维护。通过分析数据趋势,AI可以预测设备可能发生故障的时间,从而在故障发生前安排维护,减少停机时间和维修成本。
3.高级安全功能:
随着对数字系统的依赖增加,网络安全已成为一个主要问题。现代控制系统包括高级加密、多因素认证和入侵检测功能,保护敏感的工业运营免受网络威胁。
4.模块化与灵活性:
现代控制系统是模块化的,这意味着它们可以根据特定需求进行定制,随着运营的增长轻松扩展。这种灵活性使得升级和系统扩展更加容易,确保行业能够满足不断变化的需求,而无需彻底改造其基础设施。
实施先进控制系统的挑战
尽管取得了这些进步,但集成这些复杂的控制系统仍可能面临挑战:
1.高昂的初期成本:
虽然数字控制系统通过提高效率提供了长期的成本节省,但初期的成本可能很高,特别是对于需要全面改造系统的传统行业。
2.集成的复杂性:
将新的控制系统与现有设备集成可能很复杂,尤其是在基础设施较旧的环境中。确保新旧技术之间的兼容性需要仔细的规划和专业知识。
3.技能差距:
现代控制系统的复杂性意味着操作员需要先进的技术培训。公司必须投资培训计划,确保团队能够有效管理这些系统。
控制系统的未来
控制系统的未来充满希望,即将到来的技术进步将持续突破现有局限:
1.数字孪生:
数字孪生是物理系统的虚拟复制品,允许实时监控和模拟。这项技术支持预测性分析和优化,使操作员能够在现实系统中实施更改之前测试场景。
2.边缘计算:
边缘计算在设备本地处理数据,而不是完全依赖云端,它正获得越来越多的关注。这种方法提高了数据处理速度并减少了延迟,这对于实时工业应用至关重要。
3.自主系统:
随着自动化的不断进步,我们正在朝着完全自主的控制系统迈进,这些系统可以基于实时数据独立做出决策并调整流程,而无需人工干预。
结论
从手动控制面板到先进的数字系统,控制系统在提高运营效率、安全性和灵活性方面取得了长足的进步。当今集成的、支持物联网的控制系统为制造商提供了比以往更智能、更快速、更安全的运营工具。
随着数字技术的不断发展,控制系统革新行业的潜力也将持续增长。拥抱这些创新将是在日益数字化的世界中保持竞争力的关键。